Why Regular Packaging Machine Repair Is Essential for Your Business
Why Regular Packaging Machine Repair Is Essential for Your Business
Blog Article
Quick and Reliable Packaging Maker Repair Service Solutions to Minimize Downtime
In the affordable landscape of manufacturing, the efficiency of product packaging operations depends upon the dependability of equipment. Quick and trusted repair service services are vital in reducing downtime, which can result in substantial monetary losses and operational obstacles. Recognizing the significance of timely treatments and the function of specialist service technicians can transform exactly how businesses approach repair and maintenance. Browsing the myriad options offered for repair services can be tough. What elements should organizations consider to ensure they are making the appropriate choice for their operational demands?
Importance of Timely Repair Works
Timely repair work of packaging machines are essential for keeping operational effectiveness and lessening downtime. In the hectic atmosphere of production and packaging, even small breakdowns can bring about considerable delays and efficiency losses. Dealing with issues promptly guarantees that devices operate at their optimal ability, therefore securing the flow of procedures.
Moreover, normal and timely maintenance can avoid the acceleration of small problems right into major breakdowns, which commonly sustain higher repair prices and longer downtimes. A positive approach to equipment repair service not only preserves the honesty of the devices yet likewise enhances the total reliability of the assembly line.
Furthermore, prompt repair services add to the longevity of packaging equipment. Machines that are serviced without delay are less most likely to deal with too much damage, enabling businesses to optimize their investments. This is particularly important in markets where high-speed packaging is crucial, as the requirement for regular performance is vital.
Advantages of Reliable Company
Reliable company play a critical duty in ensuring the smooth procedure of product packaging devices. Their proficiency not just boosts the efficiency of repair services but likewise adds significantly to the durability of devices. Trusted company are equipped with the technical understanding and experience needed to identify concerns properly and implement efficient options quickly. This minimizes the threat of reoccuring problems and guarantees that devices operate at optimum efficiency degrees.

In addition, a trusted provider provides extensive support, including training and advice for team on equipment procedure and upkeep finest practices. This not only encourages workers however also cultivates a society of security and effectiveness within the organization. Overall, the advantages of engaging trusted company prolong beyond instant repair services, favorably affecting the whole functional workflow of packaging procedures.
Typical Product Packaging Device Concerns
In the world of product packaging procedures, various concerns can jeopardize the effectiveness and functionality of machines. One common trouble is mechanical failing, typically stemming from damage or insufficient upkeep. Parts such as gears, belts, and electric motors may fall short, resulting in break downs that halt manufacturing. An additional typical issue is imbalance, which can create jams and unequal product packaging, affecting item quality and throughput.
Electrical issues can likewise interrupt product packaging procedures. Defective circuitry or malfunctioning sensing units may lead to irregular machine habits, creating hold-ups and increased operational costs. Additionally, software application problems can prevent the machine's programming, causing functional ineffectiveness.
Irregular item circulation is an additional click over here crucial problem. This can develop from variants in item weight, dimension, or shape, which might impact the equipment's ability to deal with products precisely. Inadequate training of operators can intensify these problems, as untrained personnel might not identify very early indications of malfunction or may abuse the tools.
Resolving these usual product packaging maker problems quickly is important to keeping performance and making sure a smooth operation. Regular inspections and aggressive upkeep can considerably alleviate these issues, fostering a click this link dependable packaging setting.
Tips for Lessening Downtime
To reduce downtime in product packaging operations, executing a proactive upkeep method is important. Routinely set up upkeep checks can determine potential problems before they rise, guaranteeing machines run successfully. Developing a regimen that includes lubrication, calibration, and inspection of important components can dramatically decrease the frequency of unforeseen breakdowns.
Training team to operate equipment correctly and acknowledge early indication of breakdown can also play a crucial duty. Empowering operators with the understanding to carry out standard troubleshooting can prevent minor concerns from causing major delays. In addition, maintaining an efficient supply of important extra components can speed up repairs, as waiting on components can lead to extended downtime.
Furthermore, recording machine efficiency and maintenance activities can aid recognize patterns and recurrent troubles, permitting targeted treatments. Incorporating sophisticated monitoring technologies can supply real-time data, enabling anticipating upkeep and minimizing the threat of sudden failings.
Lastly, promoting open interaction between drivers and upkeep teams ensures that any abnormalities are quickly reported and attended to. By taking these positive actions, organizations can improve functional effectiveness and significantly decrease downtime in product packaging procedures.
Choosing the Right Repair Service
Selecting the appropriate repair service for packaging machines is a crucial decision that can dramatically impact operational effectiveness. An appropriate company guarantees that your equipment is fixed quickly, efficiently, and to the highest possible standards. Begin by assessing the supplier's experience with your specific type of packaging tools. A visit their website service technician acquainted with your equipment can diagnose problems extra precisely and execute services much more swiftly.
Next, consider the solution company's reputation. Looking for responses from various other businesses within your market can give insights right into reliability and top quality. Qualifications and collaborations with recognized devices suppliers can also suggest a dedication to excellence.
Additionally, assess their feedback time and availability. A company who can supply timely support minimizes downtime and maintains manufacturing circulation constant. It's also crucial to ask about service warranty and solution warranties, which can show the confidence the copyright has in their job.
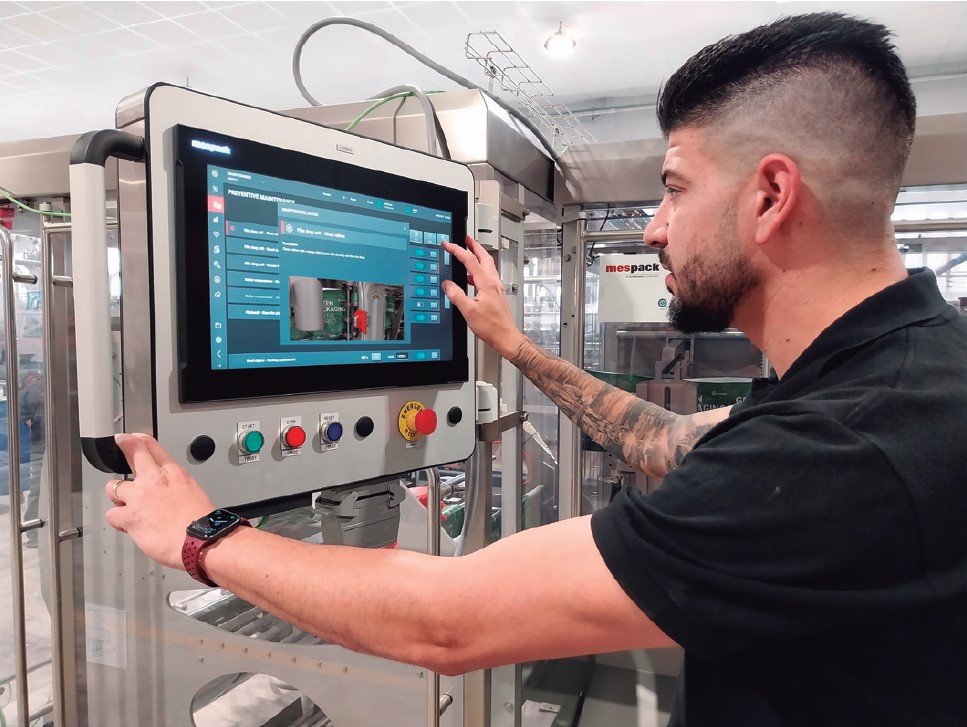
Verdict
In conclusion, the relevance of reliable and quick product packaging equipment repair services can not be overstated, as they play a vital function in reducing downtime and making sure operational effectiveness. Carrying out positive maintenance techniques and spending in staff training more boosts the long life of product packaging equipment.
Prompt fixings of packaging makers are important for preserving operational efficiency and reducing downtime.Additionally, timely repair work add to the durability of packaging machinery. Generally, the benefits of involving trusted service carriers expand past prompt repairs, favorably affecting the whole functional operations of packaging procedures.

Report this page